Reloading press designs vary, and some offer advantages, if they’re needed. Read more about which, what, and why HERE
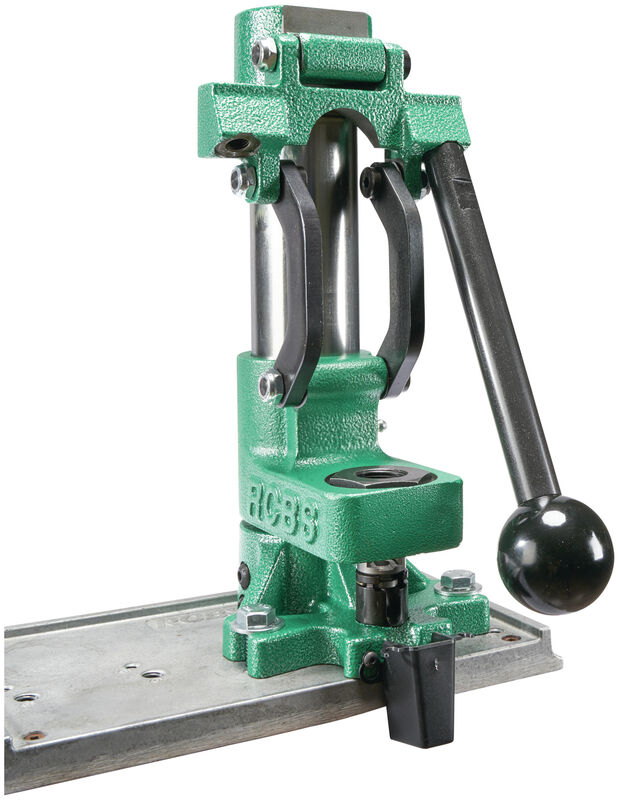
Glen Zediker
This is the last (for now) look at reloading press designs and features, and it’s all about power — leverage and linkage.
The more leverage a press can generate the less input effort from us is required in performing an operation, especially a more challenging operation like reforming cartridge cases, but that’s got another side to it. A longer stroke, and a heavier mass to move, also means more exertion on each stroke, and more time spent case to case.
Since we don’t always know the ultimately most demanding operation we’ll call on a press to perform, my advice is to err on the “stronger” side, and also on the “longer” side. I prefer a press with a shorter handle stroke (and a shorter ram stroke) because it’s less tedious to operate — but that’s true only when the press ops are not taxing. Yes, I’ll explain more: when the duties are sizing small to medium sized commercial brass cases (like .223 Rem. up to .308 Win.), seating bullets, decapping, seating primers then excess press isn’t needed. But when it’s more taxing, like in the case reforming already mentioned, and also sizing once-fired military cases, or loading for a honker like .338 Lapua, a longer ram stroke and more leverage is most welcome.
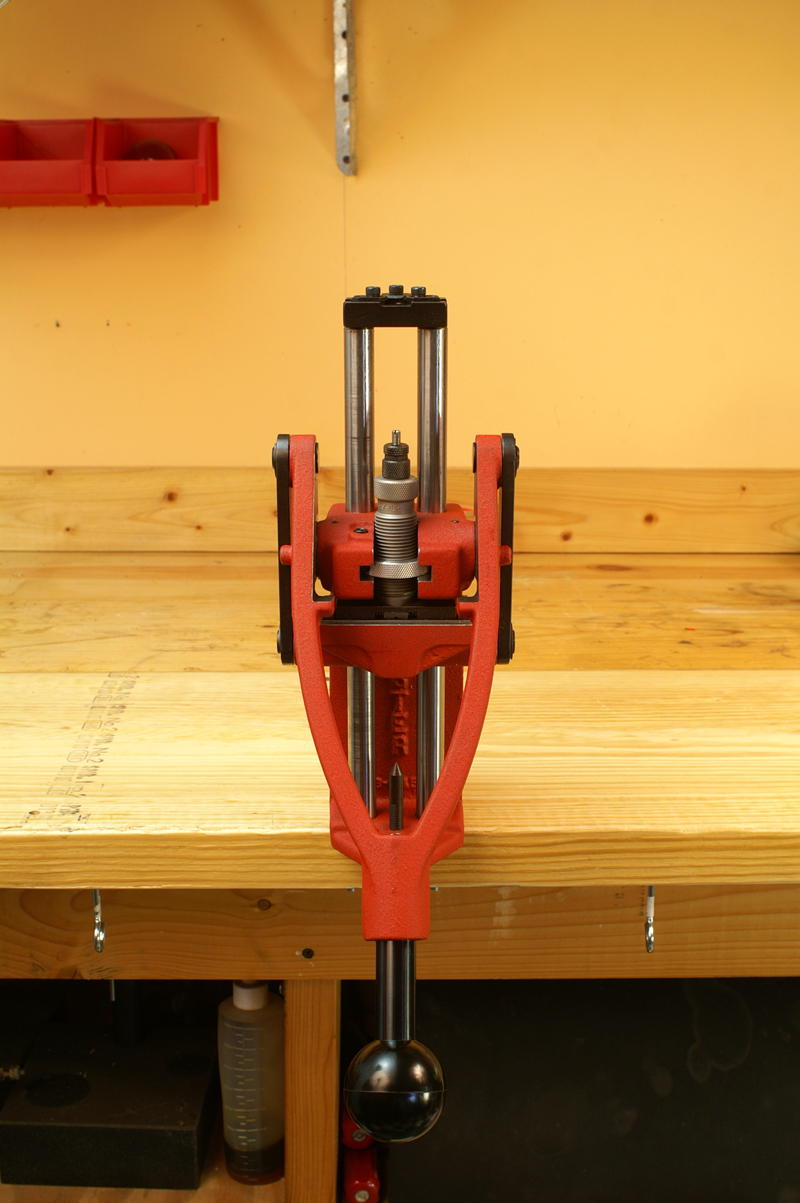
I’ve been doing all this long enough to have collected more than one press, at more than one “size,” and I’ve used them all over a good many years. The one I use the most is on the smaller, shorter end of the press spectrum, and that is only because the most of the loading I do now is decidedly not taxing. But give me a Kroger sack full of Lake City 7.62 and my Forster CoAx or Harrell’s Sportsman is getting mounted up on the bench.
Speaking of effort, case lube is decidedly important in smoothing out taxing sizing ops. I prefer a petroleum-based lube, but that’s not meant to start an argument!
There are a few different takes on the best way to design linkage (the levering mechanism that powers the ram), including those that operate more or less upside down. I’ve not used them all but have, generally, found that handle length has the biggest influence on leverage.
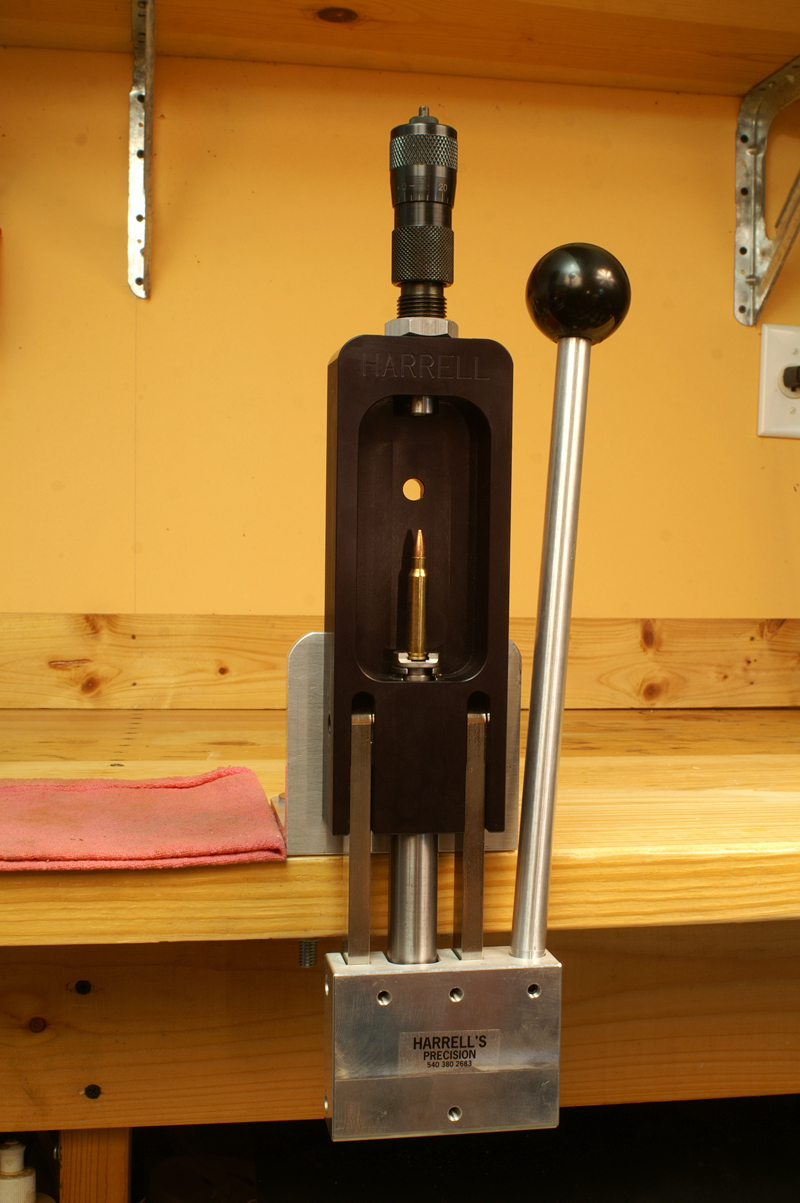
Cam Over
Speaking of linkage… Some reloading presses are designed with eccentric linkage such that it’s possible to “cam” the ram. The concept involves circular motion and linear motion, meaning that when the ram traveling in a linear path reaches full extension, the linkage which is traveling in a circular path, can move through the 0-degree mark and go to a negative degree — like a crankshaft in an engine. To get a picture of this: As the handle is moved downward to elevate the ram, the ram reaches its maximum height just short of the very limit of its travel upward, and, at the last little bit, lowers. So when the handle is all the way through its arc, the press ram is sitting a little lower. This action, called “cam over,” has essentially increased “ummph” in the linkage, and it’s done that by making contact (plus) with the die.
I’m not a fan.
Now, any substantial press, whether it has eccentric linkage or not, can produce the effect of camming-over. A Forster Co-Ax, for instance, can just about crush a chrome car bumper and doesn’t have eccentric linkage. To set up that press, any press, to cam-over, turn the die a little (1/8 turn or so) downward beyond what provides full and flush contact with the shellholder when the ram is at its full height. Then, when the press handle is fully down, the additional pressure in the last bit of the handle stroke goes toward flexing the press. Simple as that, and that is what camming-over does: flex the press. And, again, that’s true whether it has eccentric linkage or not.
Don’t do it. Just don’t.
There’s no need to cam-over a press for a case-sizing operation. It creates unnecessary stress. Dies can get deformed and bent, carbide dies can break, and the press hisself can suffer, and even break. Some defend this practice by saying presses are designed to “take it,” but eventually there’s a penalty for taking any machine to its limits, continually.
The real deal is that it’s just not necessary! Using a cartridge case headspace gage to determine sizing die positioning to get the correct amount of case shoulder setback, it’s clear that sure should occur at a point short of full contact between the die bottom and the shellholder surfaces. But, and this is important, if it’s not then trying to push a case farther up into the die by crushing the shellholder against the die isn’t going to do much. Done is done. The flexing might, maybe (maybe), increase setback 0.001.
If your sizing die doesn’t adequately set back a case shoulder, then that die has to be modified by having material ground off its bottom.
Camming-over a press is a “feel-good” measure for some folks: there’s this satisfying “ka-thunk” at the limit of press handle stroke, and that lets a loader know that they gave it all it could get. I’ve also had some claim that the stress and flex brings “everything into perfect alignment.” No it doesn’t. Alignment in a press was determined by the maker, not pressure. If your press hain’t straight, bending it more won’t help.
Cam-over has its application in some bullet making operations, but those are not on-topic here.
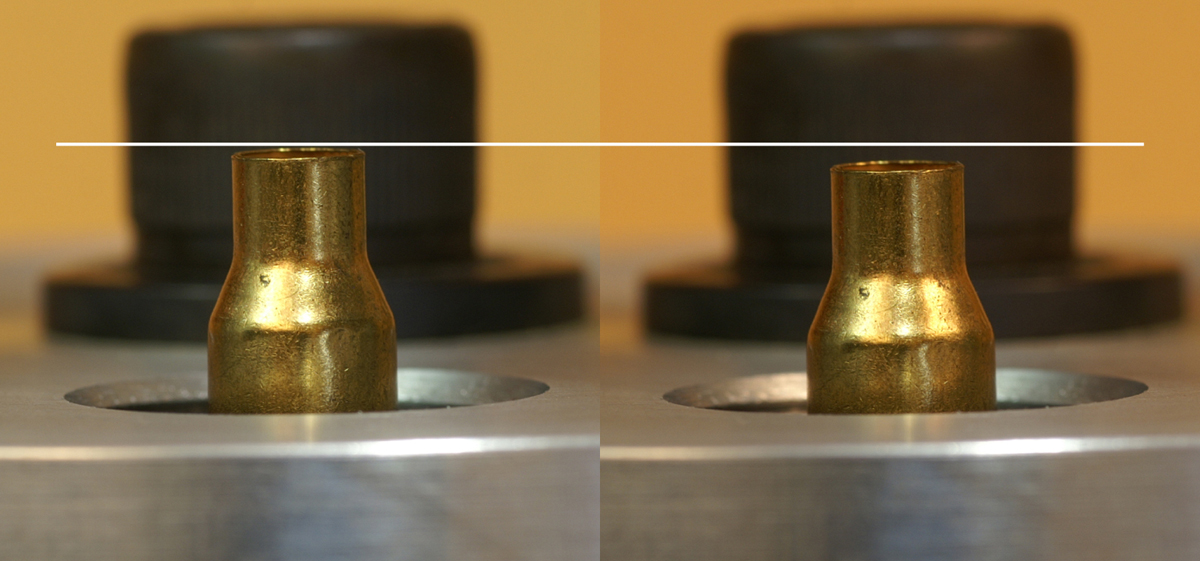
More, And Some Is Good!
To find out if you have a “cammer” run the press ram fully up (press handle fully down) and thread a die in until it touches the shellholder. Try to move the handle back down. If it won’t budge, it’s got eccentric linkage. It won’t move because the ram is trying raise again. Back out the die until the handle moves and pulls the ram away. It’s at this point where “flush” contact with a die bottom will be. As long as the shellholder is not being contacted, presses with this sort of linkage have a smooth feel to them and do a little more positive job of sizing. In effect, the case gets sized twice (the ram elevates again just as the press handle is lowered). Linkage, either way, has zero effect on setting up a die because you measure what you get anyhow, and adjust the die accordingly, after you see what it is that you got.
The preceding is a adapted from information contained in from Glen’s books Top-Grade Ammo and Handloading For Competition. Available HERE at Midsouth Shooters Supply. Visit ZedikerPublishing.com for more information on the book itself, and also free article downloads.