Five tips to reduce shot-to-shot bullet velocity deviation. READ MORE
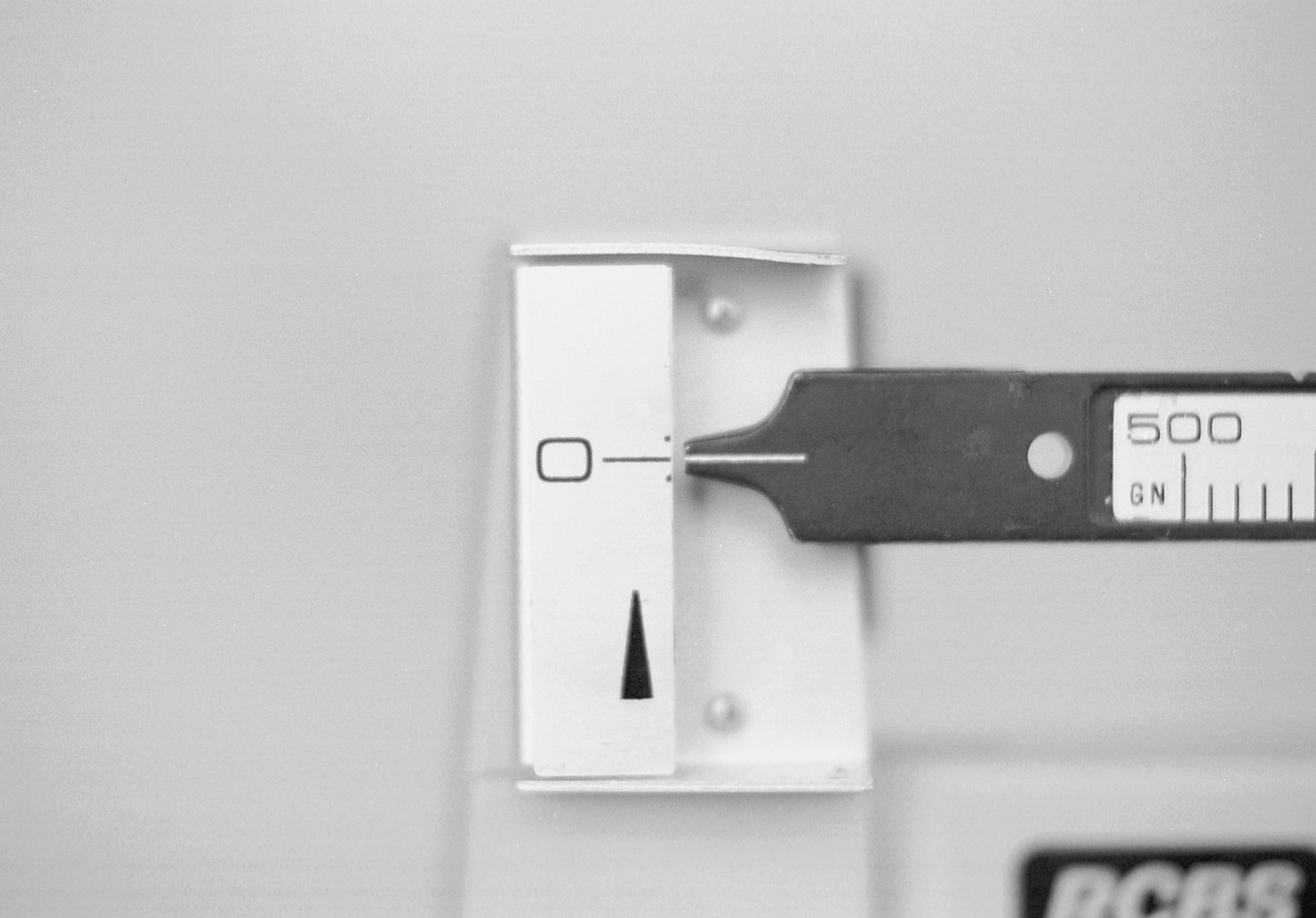
Glen Zediker
I’ve spent the last two editions on velocity variations, and this one will offer some ideas on how to get yours as low as possible.
Consistent Propellant Charge
This comes first to mind, and probably comes first in most everyone’s mind, and that’s because it makes the most “sense.” Sure enough, given the effect on velocity from a tenth or two grain variation in propellant, eliminating that variable clearly takes a big step toward improving consistency.
Now comes the big question: Throw or weigh? That one there is another complete article, but the short course is, “it depends.” Bad answer! I know, but there’re more coming in a bit to add to either confusion or clarity, depending on experience. Overall, I’ll say “weigh.”
I say “weigh” because that goes a long way toward eliminating inconsistent amounts of propellant as a factor. I also say weigh because of the previously mentioned undeniable effect of haphazard propellant levels, and weighing each charge should eliminate that. Do, however, make sure that the scale is reliable. I still use an old-school beam scale. A good deal of trials and tests have not given me the confidence I need to have in many electronic scales. The short answer to satisfaction, again from my experience, is that you’ll likely get best, or at least better, results from a scale that ranges upward in cost from the “mid-priced” units, and decidedly better performance compared to the lower-priced models. I’ll also say the same for the scale-based dispensing devices on the market. I’ve used a couple that my meter beat, and a couple that were impressively accurate over a lengthy session.
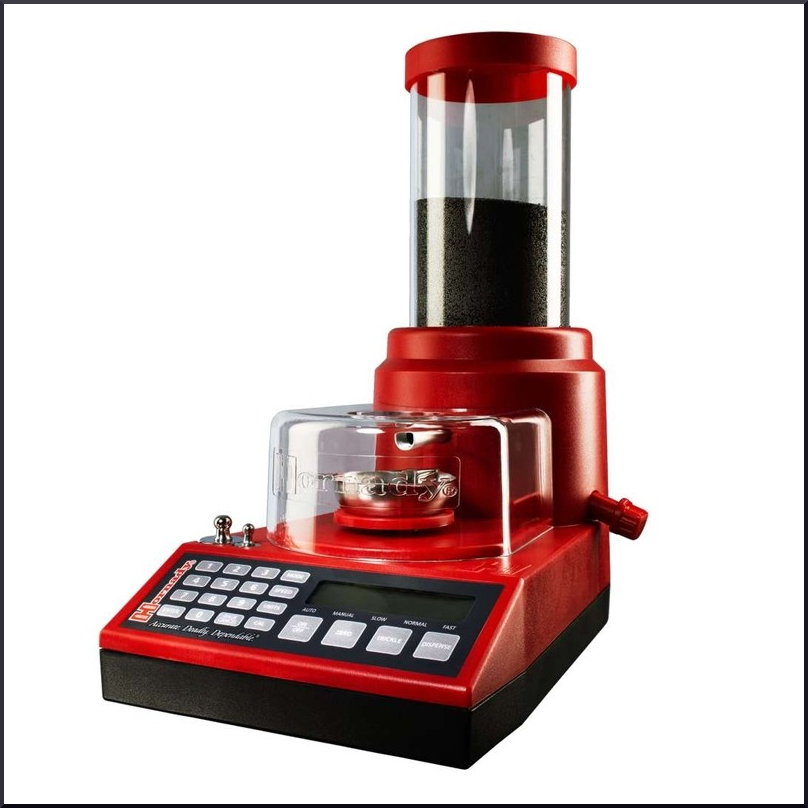
Ignition Enhancement
Numbers 2 and 3 on my 5-point list involve the primer — ignition. This is a crucial point in the life of a flying bullet. If the primer is delivering a consistent flash to ignite the propellant column, then said column will ignite more consistently.
Uniforming the primer pocket can help. The main thing this trick accomplishes is a flat-bottomed primer pocket. The tool faces the bottom of the pocket to squareness and also cuts the entire bottom of the pocket to squareness. Most primer pockets are formed using a punch and that leaves a radius on the “corners,” resulting in a bowl-shape. Since primers are flat, they don’t seat correctly and as designed unless the primer pocket is flat. And, if the primer pocket is flat then the primer can be seated fully, which means that the anvil “feet” make correct, full contact.
If the primer isn’t seated flat and flush then some energy from the firing pin gets absorbed in finishing the primer seating, and that leads to a softer hit, and less (perfect) consistency in ignition. Yes. It’s tiny, but so is all of this!
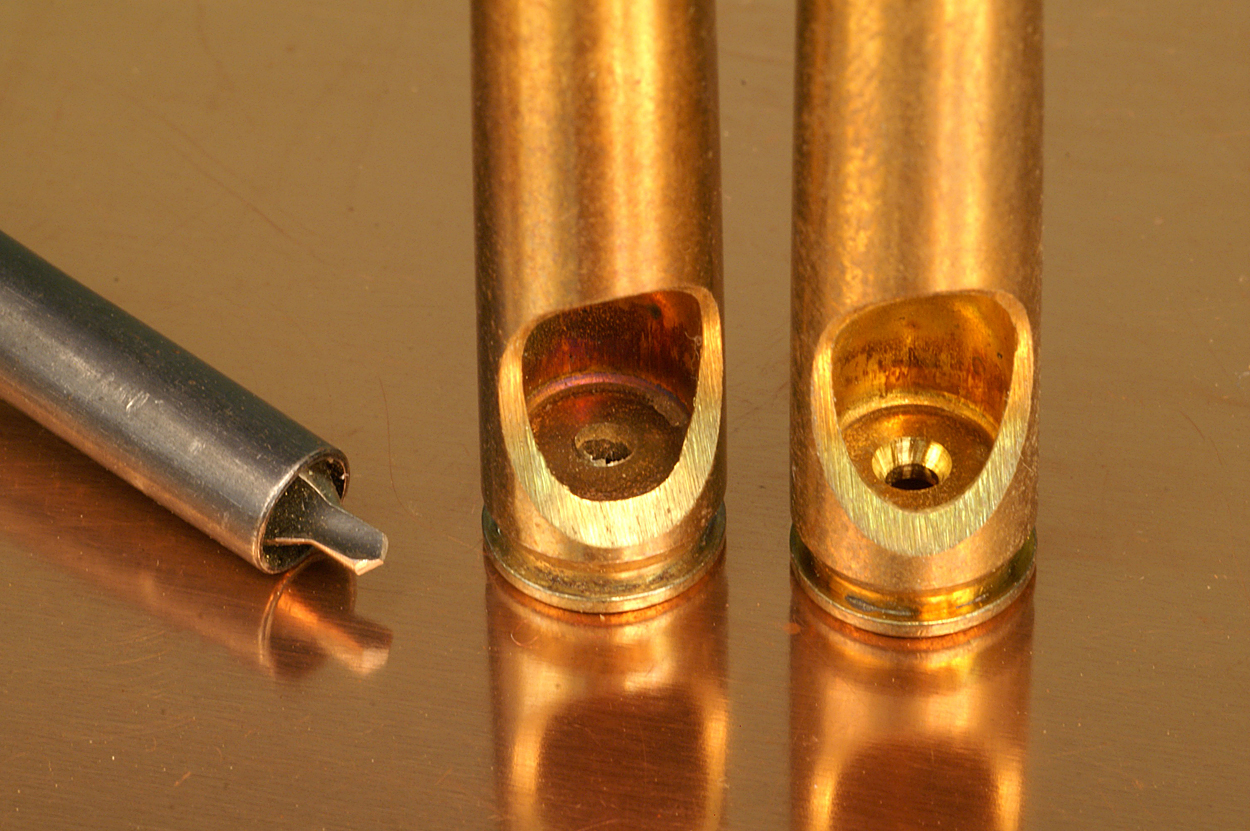
Uniforming the primer flash hole is another trick that honestly “works” to improve velocity consistency. This is another usually punched process and can leave a burr visible on the inside of a case. A uniforming tool removes this burr and, depending on the tool design or its adjustment (if possible) will also create a little funneled area believed to better spread the initial flash to ignite the powder column. Some worry about losing metal in this area, but it will not weaken the case in any detrimental fashion.
Consistent Bullet Grip
Bullet “release” has to be consistent for the combustion behind it driving it forward to be consistent. First, that means the case neck walls should ideally be consistent so the case neck cylinder will be sized to a consistent dimension. The “spring back” in brass means thinner or thicker walls respond differently to the same dimension sizing apparatus. Again, this is a tiny thing, but they all add up.
Further, myself and a good many others have found that we usually see better shot-to-shot velocity consistency with a little more, not a little less, case neck grip, or bullet retention, however you prefer to call it. By “grip,” which some also often call “case neck tension,” I’m talking about the difference between the sized case neck inside diameter and the bullet diameter. This is something that my friend and associate, David Tubb, has done a good deal of experimentation with, as have I.
We both found that best results, again meaning best velocity consistency, came at more than 0.002 inches difference. I routinely use 0.004 for my competition loads.
One way to improve the consistency in grip is using a mandrel as a separate operation. A mandrel is pretty much a sizing button or expander that’s got a longer surface area, and, of course, is precisely sized. The idea is to use the mandrel on a case neck that is sized at least 0.003 inches smaller than the mandrel, run the mandrel into the case neck for a 5-count (important) and then withdraw it.
Another thing: I’ve got all the means but not yet had the time to experiment with adhesives. Right: That’s glue between the bullet and the case neck inside. Varying bond-strength glues have been used in honking big cartridges for military use for years and one of the pretty well demonstrated benefits is increased velocity consistency. This is a new area for the handloader and I hope to have some more information about it later on.
Last
I really don’t like it when we sometimes (and honestly) say that it’s “more art than science.” We say that when there’s a predictable or at least reproducible combination of things that give great results. In handloading that’s something like very good accuracy and very small shot-to-shot velocity variations.
Of course it’s science! But it’s just not that well understood, meaning it’s not precisely predictable, or at least not by me and most who recite that mantra. There is a combination of case, propellant, primer, bullet, and barrel that appears magic compared to some of the other things we’ve tried. It’s all a system. Since we’ve got the barrel and it is what it is, propellant and primer are the main variables, and of course we can try different cases. I believe that it’s case volume as part of the system that has its influence on performance.
Back to the first point, ultimately the answer to the “throw or weigh” question comes as a combination of the precision of the meter and the choice of propellant. I don’t weigh charges, or not making up the loads I settled on for use in tournaments, and that’s because I see zero difference in on-target results, and that starts with seeing zero difference in shot-to-shot velocity readings in testing. I, however, have seen radical differences in on-target results with other combinations comparing weighed and thrown. However! Those loads still didn’t make my cut because, overall, the velocity consistency just wasn’t there in the first place. Folks I can tell you absolutely that just weighing each charge does in no way mean you’re going to get suitable spreads with any old gunpowder. The ultimate answer to attaining tiny shot-to-shot velocity variations, and tiny shot groups, comes from experience in doing your own testing. That’s a “said nothing” statement, but there has to be a willingness to experiment.
Beyond only experimentation, though, I think these few tips will help ensure you’re getting the best that combination can give you.
This article is adapted from Glen’s book, Handloading For Competition, available at Midsouth HERE. For more information on that and other books by Glen, visit ZedikerPublishing.com