Reloading problem? First make sure it’s not your tools… Here are a few things that can happen, and how to correct them.
Glen Zediker
Over years and years (and years) I’ve encountered a few factory-faulty sizing and seating dies, and associated pieces-parts. It’s not at all common, but it happens, or has happened, enough that I wanted to share a few stories as to what these problems come from, and how to identify (and correct) them.
As has been my norm here of late, yep: got a phone call from a fellow having problems with a new 28 Nosler. Took a while to get through this one… Turned out that the sizing die was the culprit. Wasn’t easy to sleuth but there’s a Zen tenet that paraphrases to this: If you’re not sure what something is, then carefully consider all the things that it is not; what’s left is the answer…
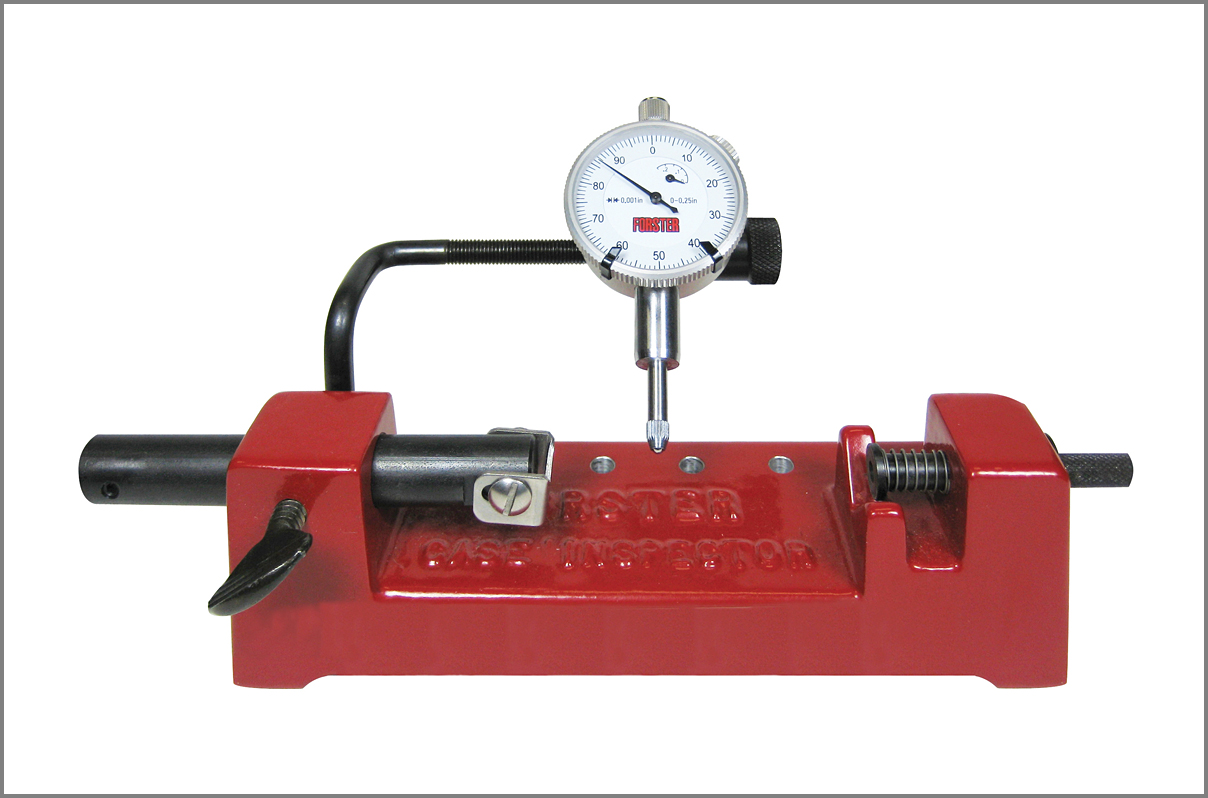
By the way, I’m not going to mention brand names for one good reason: I’ve seen or been presented with issues in dies from every major maker.
Sizing die problems I have either encountered first-hand or been witness to via my circle have most often been a full-length die that will not adequately set a case shoulder back where we want to take it. Conversely, it’s much more common to have a die that’s erring on the more extreme end of that, and erring toward “too much” sizing potential is logically a direction a die maker might take to accommodate more circumstances. Once the shellholder is making full and flush contact with the die bottom, that’s all she wrote. Continuing to turn the die body downward does nothing but stress the press and possibly damage the die. To get the case farther up into the die, either thin the shellholder top surface or grind the bottom of the die hisself. Neither are hand-tool operations! Get to a local gunsmith or machinist.
Look at a hair from your head and that’s ballpark 0.004-0.006 inches. It doesn’t take much at all to make the difference between smooth function and a bolt that won’t close.
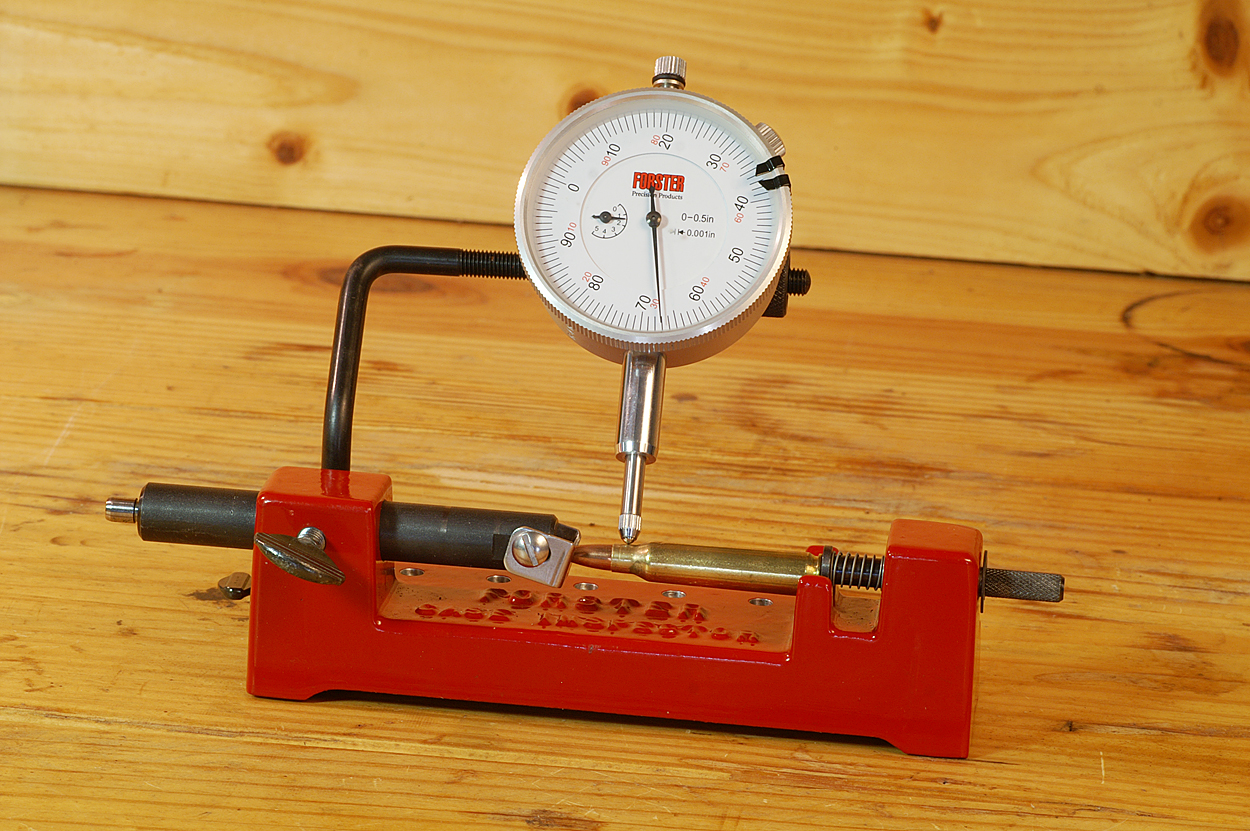
Check out Midsouth tools HERE
Most sizing dies are reamed one-piece, one-shot like a rifle chamber; however, that’s not always the method. Some are done in two or more steps, using two or more cutting tools. Clearly, consistency and correctness favors the one-piece reamer. Assuming that the reamer is correct and correctly used. I have encountered one die that just wasn’t concentric, body chamber to neck area. I figured that one out by sizing without the expander and checking runout, and also by finding that I could shift off-center axis by rotating the (marked) case and running through again. Normally, sizing a case without the expander in place results in a case that runs flat-line on a concentricity fixture. Reason is primarily because any inconsistency in the case neck walls get “pushed” to the inside case neck. But if there’s wobble in a case that’s been sized sans expander, then, son, you got a die problem.
A bent or bowed expander stem will, not can, result in an expander that’s going to cock the case neck one direction. I watch for that when I polish the expander button. As described here before, that process involves chucking the stem (lightly) in an electric drill and spinning the ball against some wet emery to give the ball a shine. If it’s wobbling during this operation, that’s a problem.
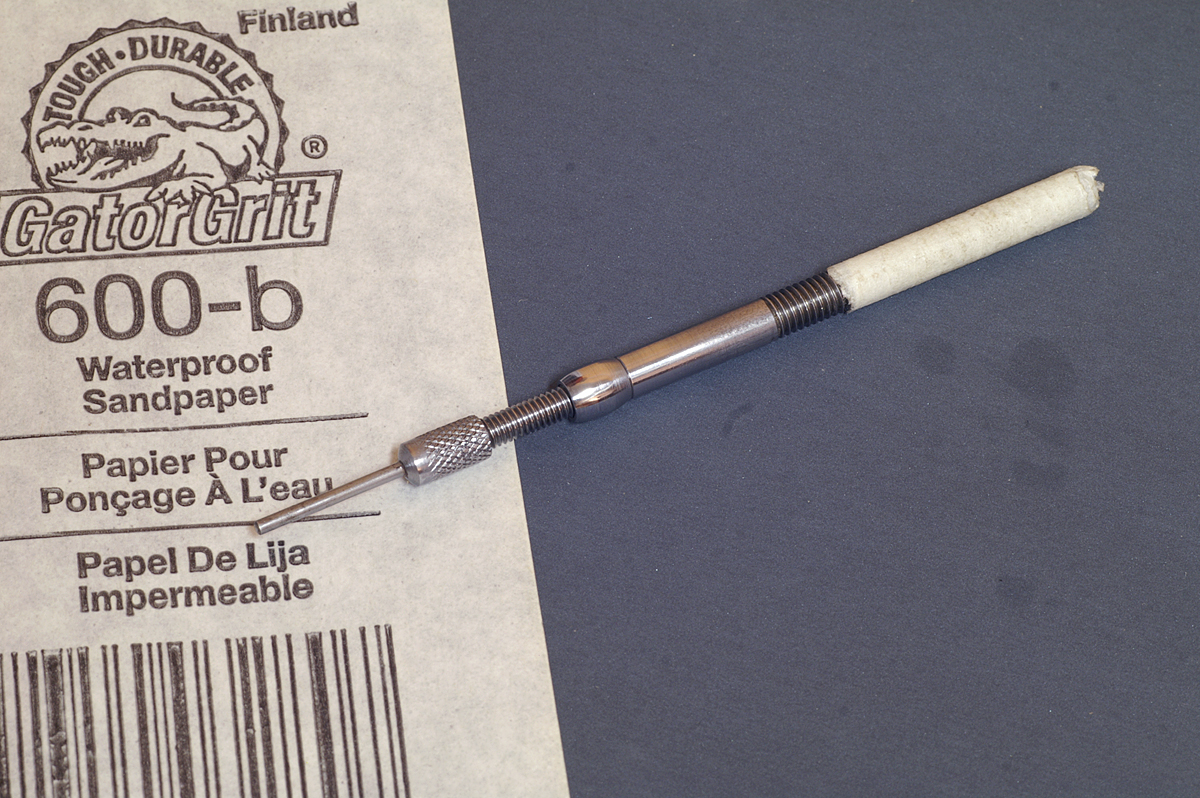
Seating die issues, in my experience, usually revolve around plain old straightness of the seating stem, and, once, the concentricity of the reamed case body area. If you have a seating die that increases runout compared to what a concentricity fixture showed on the sized case neck, it needs looked into. Additionally, always (always) check to make sure the seating plug (the area that fits over the bullet to push it into the case neck) is deep enough the the bullet tip does not make contact with the inside of the plug. That’s a sure way to get a bullet tipped off kilter.
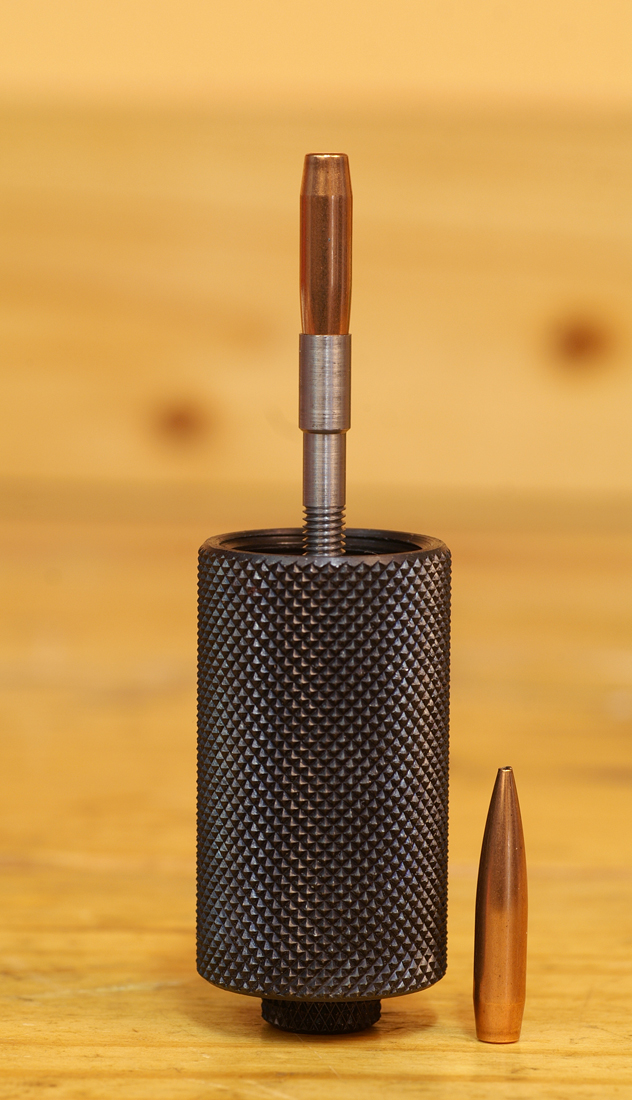
Now. Most importantly: What to do if you suspect a tooling problem? Short answer is: SEND IT BACK. Don’t accept it. I know of no maker who won’t profusely apologize and promptly return a new one. The fixes I mentioned are for those who prefer to solve such issues, and also for those who have the means to effect repairs. The point to this article mostly is to be aware that problems can and do exist, and don’t accept them, whichever direction you seek for the solution.
No matter how precisely a die maker produced the parts, there is and will be some gap in threaded pieces. This can disguise itself as a “die” problem, but it’s really not. It’s a set-up problem. I did an article a good while back here on a few ideas on improving tool/case alignment via some set-up tricks, and maybe that should be the next topic under the Reloaders Corner banner.
The information in this article is from Glen’s newest book, Top-Grade Ammo, available HERE at Midsouth. Also check HERE for more information about this and other publications from Zediker Publishing.