Accuracy matters! Now here’s what matters to accuracy… This article discusses 5 essential steps that pay off big.
Glen Zediker
Last time I wrote a little “essay” on the importance of accuracy and a few ideas on why it matters and how to judge it. That’s all well and good, but the part I knowingly left out was to say more about “how” to get the most of it. Here’s a few points that, over a many-many years, have proven themselves to me to improve the quality of on-target perforations, and, to make sure I’m clear, that is manifested by smaller-diameter shot groups. There are a plenty of others who agree with these tips. There are plenty of others who might not agree with all of it, and even a few more who would love to add their own “can’t miss” components to this mix. But here are mine.
ONE: After-the-fact concentricity. By that I mean actually checking loaded rounds on a runout indicator. Concentricity is pretty much the goal for sizing, seating, and neck-related case-prep steps, like outside case neck turning. However! All those things are done to help support concentricity, but not a one of them is concentricity.
Concentricty is the centered relationship of all influential circles in a cartridge case, with the reason that a more concentric round will have its bullet looking down dead center into the rifle bore: ultimately, if the loaded round spins “flat-line” it will shoot better than those that don’t.
It starts with brass selection and then likely also segregation. Then it moves on to the quality of tool alignment.
I have checked enough factory-loaded rounds though a concentricity fixture, and those that show the best group the best; even if the overall group from random selections is so-so, “flatliners” shoot smaller.
Check out Midsouth products HERE
TWO: Inside flash hole deburring. I know I’ve mentioned this before, but this simple and easy step shows up on target next firing on thusly-prepped cases. It improves propellant ignition consistency and, depending on the tool used, also ignition efficiency.
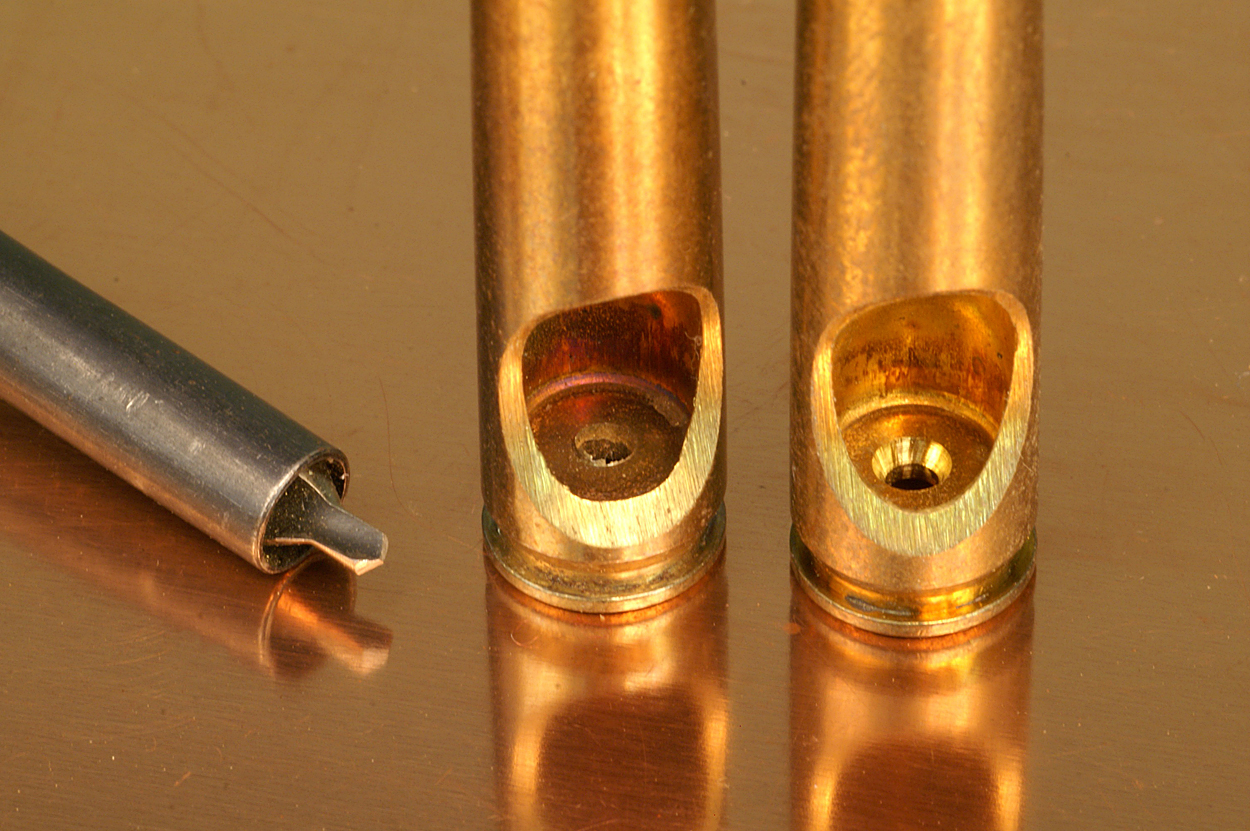
There’s a burr inside most cases that resulted from manufacture (with only a few drill-cut exceptions, like Lapua, cartridge case manufacturers punch the flash hole). This burr is variable in size and scope, but it acts as a block to the spread of primer flash, and it’s redirecting or misdirecting the flash at the same time.
It only has to be done once. Ever.
Check out Midsouth products HERE
THREE: Primer pocket uniforming. This helps because it lets you set each primer the same, and also fully. The reason is that it squares the “edges” or corners of what otherwise is a slightly bowl-shaped cylinder. A perfectly seated primer is sitting square and flush on the bottom of the pocket, with its anvil legs compressed. This “loads” the compound for rapid and consistent ignition. If the primer isn’t seated fully then the firing pin finishes that job before detonation. That creates what equate to time variables — inefficiency.
Funny, but clean primer pockets don’t shoot any better than dirty pockets. What matters is flat pockets.
Check out Midsouth products HERE
FOUR: Consistent case sizing. There is a widespread fear, especially among some “accuracy” fanatics, about sizing ops. There’s also a lot misunderstood about full-length sizing versus neck-only sizing and so on. But. What matters is that, whichever tooling and how much sizing the cases are treated to, it needs to produce dead-same cases. Consistent case expansion dynamics is not often talked about, but it’s influential, especially on longer-range rounds. Just in general, going a little on the “light” side with sizing might seem like a good idea (less stress, less working the metal, etc.) but it can also lead to round-to-round inconsistencies. My belief is that it’s better to be more “positive” in sizing ops, and by that I mean to reduce a case neck 0.003 inches rather than 0.001 prior to seating a bullet. Get all the case shoulders the same height. Running extra-light case neck tension and leaving case shoulders where they emerged last firing may not reproduce round-to-round consistency, unless the rifle chamber was perfect and the cases were too. A little more sizing works the best for the most of us in the most rifles.
FIVE: Invest in a good seating die. No doubt: the bullet seating operation is the “last thing” that happens and it’s also the one thing that can corrupt the care and treatment given to the quality of the loaded round prior. A sleeve-style seater, well machined, goes a whopping long ways toward preserving alignment, and, therefore, concentricity. Also make sure that the stem in yours comes to rest well down onto the bullet ogive, and, above all else, is not contacting the bullet tip! That will wreck a round.
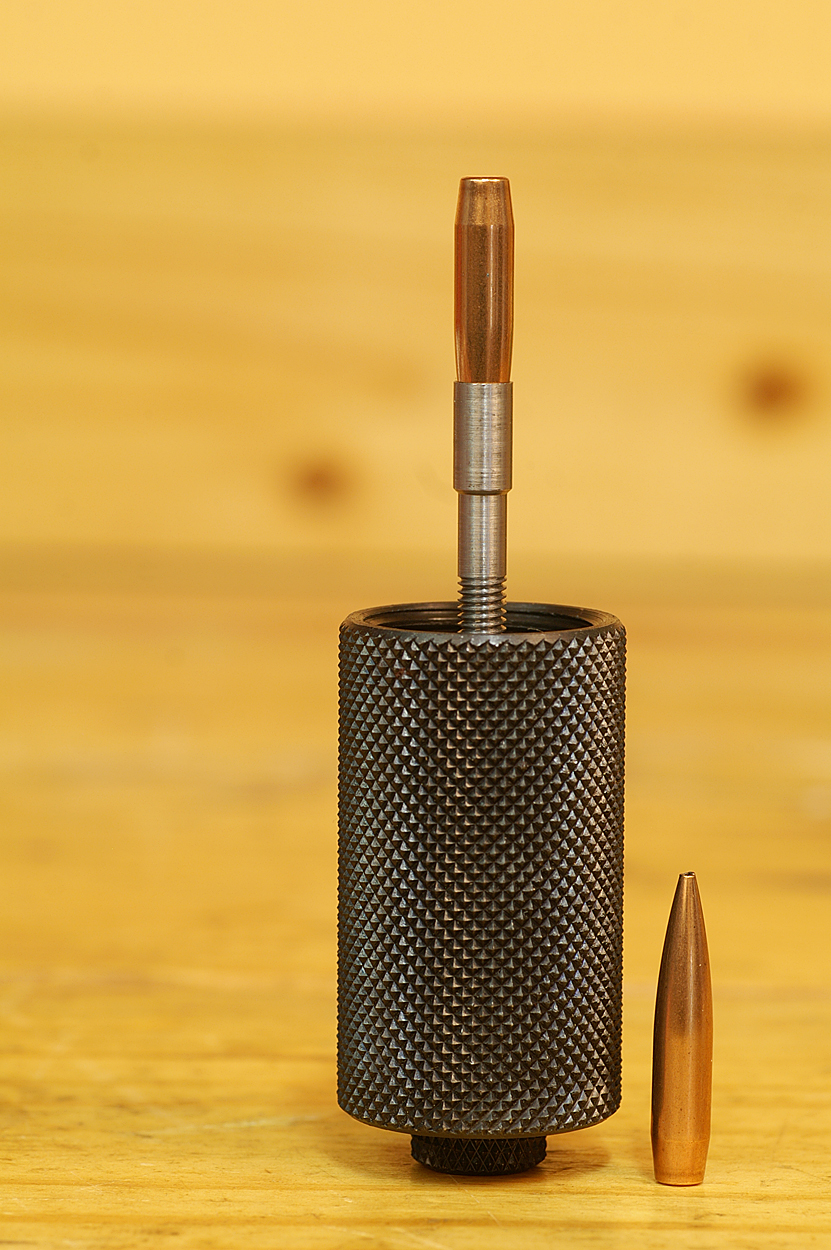
Check out Midsouth products HERE
This article is adapted from Glen’s newest book, Top-Grade Ammo, available at Midsouth HERE. For more information on that and other books by Glen, visit ZedikerPublishing.com