Bullet coatings promise better performance, but are they the right choice for you? Find out.
Glen Zediker
There are a few bullet coatings available, and Moly (MoS2: molybdenum-disulfide) is the best known, and also the most notorious. More in a bit.
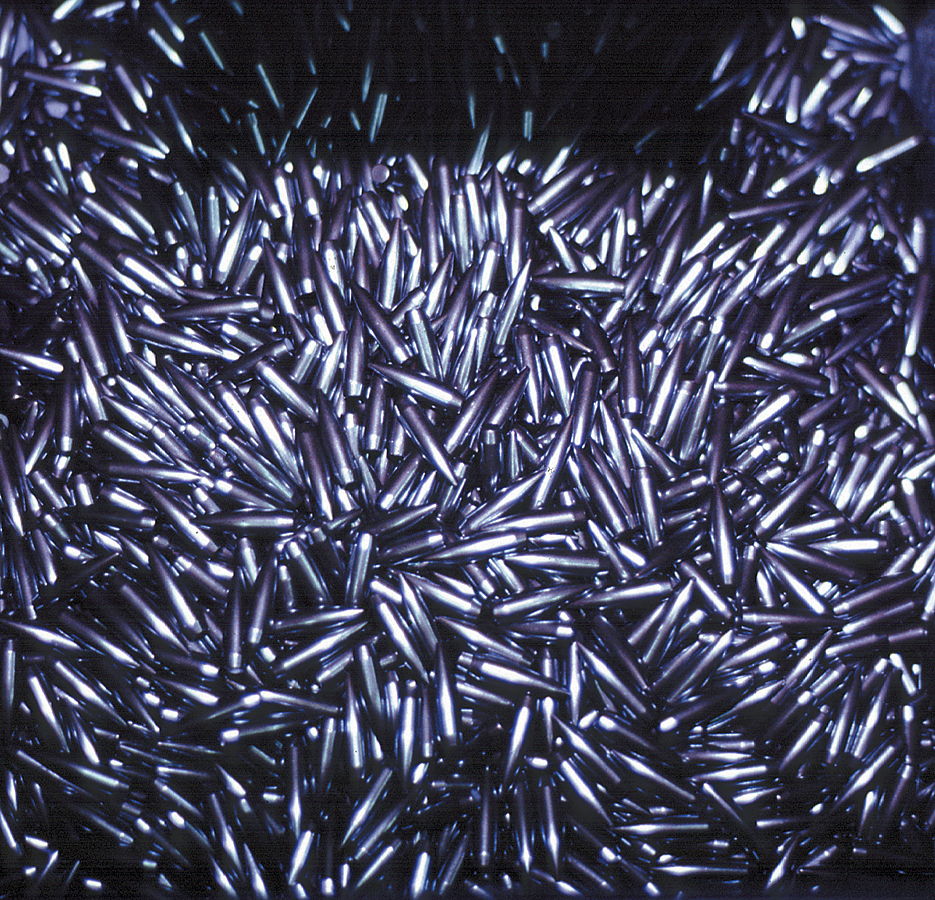
First, here’s how and why bullet coating works: Fire a coated bullet and a bare bullet using the same propellant charge. The coated bullet will go slower. However. The pressure will be lower. The reason is easy to figure: the increased lubrication reduces friction, resistance to movement, especially upon entry into the bore. It gets kind of a head start. The deal is that the pressure drops relatively more than the bullet speed, so, the bullet speed can be increased by adding more propellant and still have the same level of pressure. Win. Win. And, since there’s what amounts to a barrier between the bullet jacket and the barrel steel, the promise of more accurate rounds between cleanings is all true too. The bullet jacket isn’t leaving much of itself behind on the bore.
Among competitive shooters there was a huge shift toward coated bullets a few years back, but they’ve since fallen from favor for many. It wasn’t because they don’t perform well, because they do, but there are ancillary, and important, liabilities. Mostly: moly-coated bullets can corrode barrel steel, including stainless. Molybdenum disulfide outgases (outgas is the release of an occluded gas vapor that was part of the compound; a state change, pretty much) at temperatures lower than firing temperatures, and that creates a residue that, when mixed with water (moisture from condensation included, like what happens after firing), is pretty much sulfuric acid. Yikes. Right. If a moly-coated barrel is cleaned (correctly) each use, no problems. But one of the big draws is the potential to get literally hundreds of rounds, on zero, before the barrel needed cleaning. After a conventional cleaning (solvent and brush) it also takes time, which is rounds through the barrel, before zero will return.
I am a fan of coated bullets, and they’ve convincingly demonstrated their superiority to me after many thousands of rounds reaping rewards from the ballistic advantages. The improvement can be significant, and some bullets in particular escalate in performance more than others. Shorter bearing surface designs, by my notes, get that much more additional speed with no pressure trade-offs. Coating seems to have a disproportionately positive effect on thinner-skinned bullets, for reasons that likewise are clear. The effect here is smaller group sizes. Anything with a “J4” jacket responds well to coating (common in custom bullets).
My solution to the worries about moly was, as suggested, simply to clean the barrel each time back from the range and, also, to change my cleaning method to better accommodate the residue composition. More in a bit.
I don’t use moly any more, though. I’ve switched to Boron Nitride (BN) because it has all the advantages with none of the drawbacks, so far. BN is virtually the same in its effects as moly, based on my notes (same level of velocity drop and subsequent future increase). It’s easy to apply using a vibratory-style case cleaner.

I do not recommend any sort of lubrication inside a barrel, not for a promise of increased bullet performance. PFTE, for instance, has been touted as a great “break-in” agent for a barrel. Some use it after each cleaning to prep a barrel. Well. When it outgases, and it does outgas, it releases fluorine, a very powerful eater of all things metal.
Cleaning: Don’t use copper solvent with moly! The ingredients don’t mix well. Use only petroleum-based solvent. I switched to Kroil pentrating oil in conjuction with something like USP Bore Paste, JB Bore Compound, or similar (abrasive paste-type formulations). No room here now to convince anyone that abrasives are a safe and wise choice, but used correctly they are both. “Correctly” means a rod guide, stainless-steel rod, and keeping the rod shaft clean each pass. With that combination the bore is being protected against corrosion and the residues get gone, and, of huge importance, zero returns right away.

Last on this: Just in the same as how I do not recommend “mixing” bullets or propellants through the same barrel, same day, coatings are pretty much the same. Zero will, not can, change for the number of rounds it takes to “re-season” the barrel. If you use it, use it.
I’ve seen great gaps in the quality of coated bullet finishes. Factory-coated bullets are the way to go. It’s tough to get a good job at home, and the reason is the carnuba wax application is temperature sensitive, and also because commercial coaters use industrial-level tumblers to apply the powder. The wax is necessary to avoid a smudgy mess just from handling the bullets. If you want to do it yourself, make sure the bullets are cleaned before application. Likewise, moly can build up in a bullet seating die so clean it out every now and again.

The preceding was adapted from Glen’s newest book, Top-Grade Ammo, available here at Midsouth. For more information on this book, and others, plus articles and information for download, visit ZedikerPublishing.com