For the perfectionist! Here’s a look at an often misunderstood and widely feared case-preparation step. It’s really not all that bad! Keep reading to learn what and why.
Glen D. Zediker
Outside cartridge case neck turning is a bench-top machine-shop-style operation. It is the only way to substantively improve case neck wall consistency. This is done via material removal using an outside case neck turning appliance. The outside neck turner shaves down the “high spots” around the neck circumference. That makes the neck walls more uniform in thickness. It’s a cutter and a gap, and that gap determines the case neck wall thickness. It’s finite.
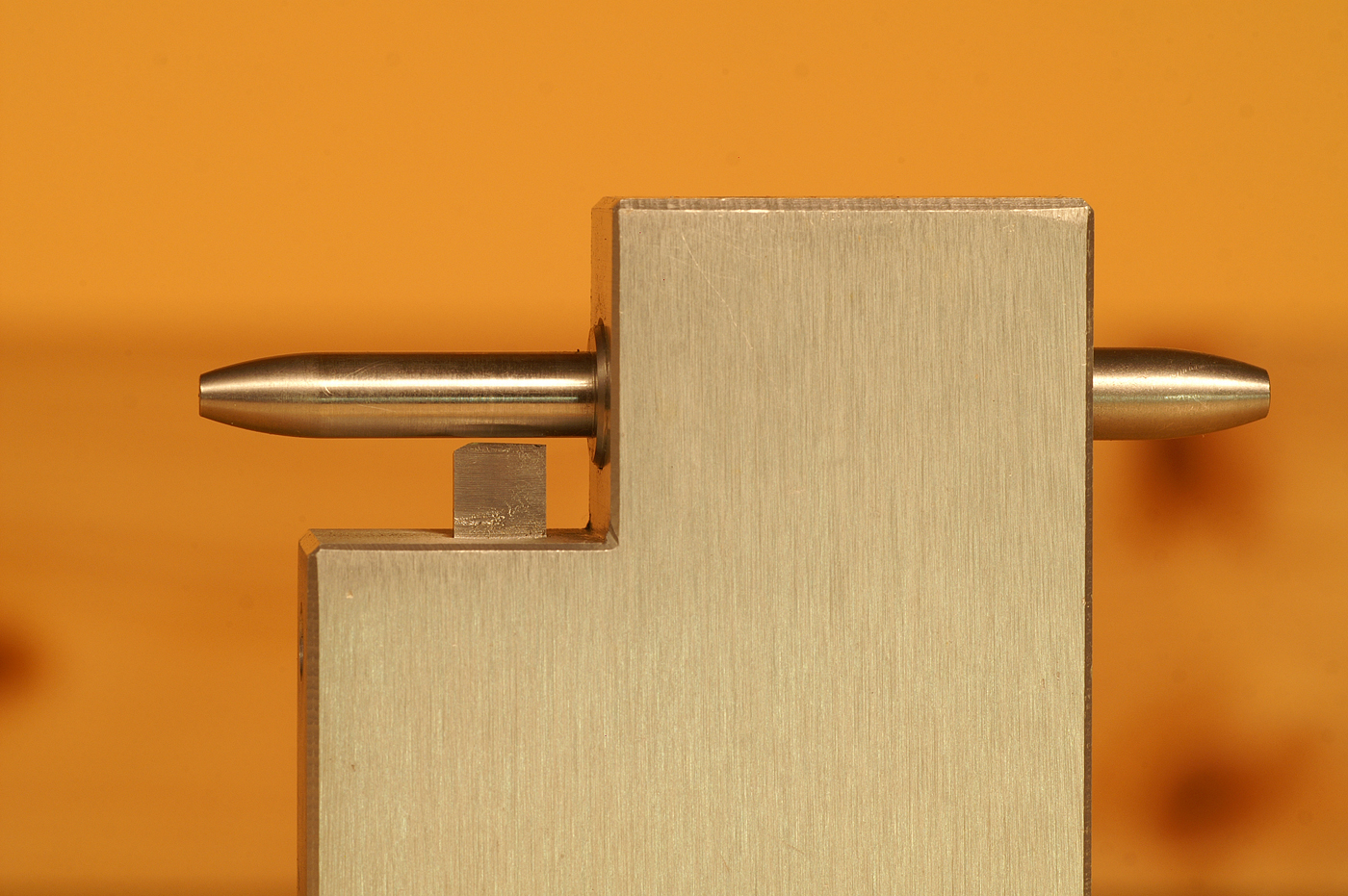
It’s pretty well agreed on and accepted that concentric relationships mean better accuracy. Getting the bullet sitting dead center in a rifle bore means that the case neck must be “straight.” A “straight” case neck results from consistent neck wall thickness. And that’s because inconsistent wall thickness creates an off-center case neck cylinder when the bullet is seated. Consistent neck walls result in a center that’s concentric (if the tooling supports it).
This is a tedious ticky operation. If you are going to turn case necks, get what you think you are from it. The only tools I’ve used thus far that do a precise job of this op are the “hand-held” turners. The lower degree of tolerance is, as with many things, the reason. A tight fit between the mandrel that goes inside the case neck and the case neck inside diameter makes for a more precise operation. The mandrel and the cutter gap will be consistent and precisely adjustable; therefore, so too will be the resultant wall thickness. The first step is to size the case neck with an expanding mandrel to fit the mandrel on the turner. The higher-speed tools, such as those that operate under power or via a crank-style base rely on some other means to locate and fix the center of the case neck. That’s not to say better is not better, because it always is. Again, it’s degrees.
Use new brass!
I have a Gracey power turner that works so fast there no real reasons not to use it for every case. It, yes, without a doubt can make a case neck better. The Forster neck turning attachment that fits the Forster trimmer base unit (same used for case trimming, and other ops) fits the same description, as does the Horndady LNL tool. These are fast enough and easy enough, and the investment will improve wall thickness uniformity. Point is, if you want to turn each case neck you choose to 0.0095 inches, you’ll need a hand tool. And a micrometer. And time. With a hand tool, the job itself is not terribly difficult or slow, but adding in the initial neck sizing op and then another sizing afterward with the usual die, it’s steps.
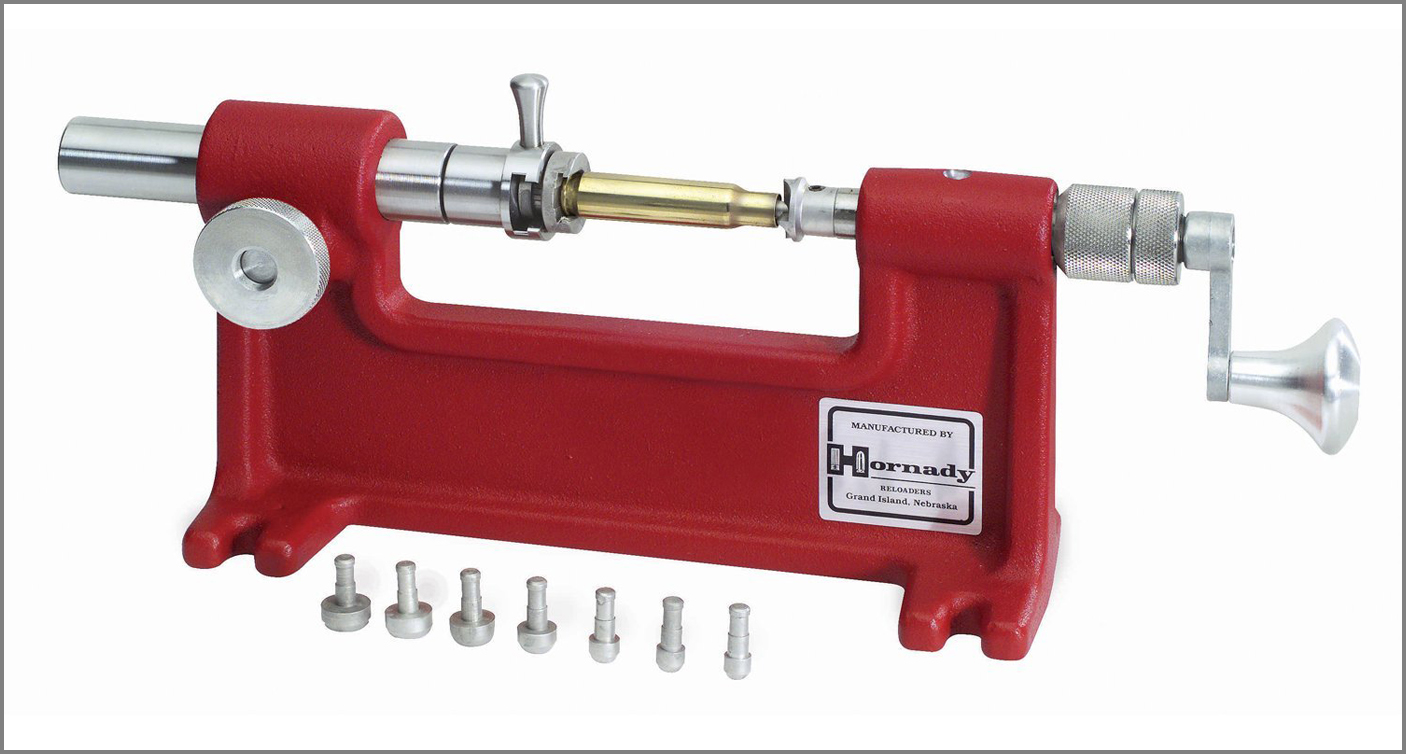
There’s a good question to answer and it involves the tolerance you’re willing to accept: perfection has a price. If the cutter head is adjusted to remove metal from the entire surface of the case neck, that means the wall thickness will be universally reduced. And that means you’ll now need to examine and possibly change your sizing setup to regain adequate post-sizing dimensions to secure a bullet. Using a routine sizer, the neck cylinder outside will get reduced to the same diameter as a case with thicker neck walls, but the case neck inside diameter will be larger because the walls are thinner. Depending on the expander diameter used in the die, the net result might be a case neck that retains an overly-large i.d. It’s just math. But make sure you work the numbers though.
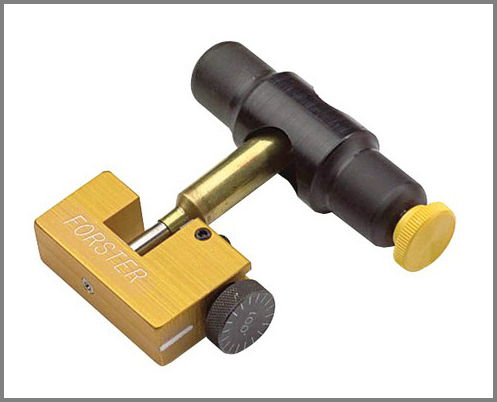
I never aim to turn the full circumference surface area around a case neck. The reason is that means adjusting the tool to produce thinner than “blueprints.” The idea, for me, is to erase the inconsistencies that remain in my sorted brass: clean them up. For example, let’s say that, after measuring enough places on enough cases, I determine that a brass manufacturer intended this tubing to be 0.011 inches (that was the “blueprint”), that then defines the cutting depth limit I’ll set my turner to deliver.
If you do turn case necks, make sure to continue cutting a little ways down onto the case shoulder (if the cutter design allows this, it needs to have an angle incorporated for this purpose). This helps stay off the formation of a case neck donut. Works wonders.
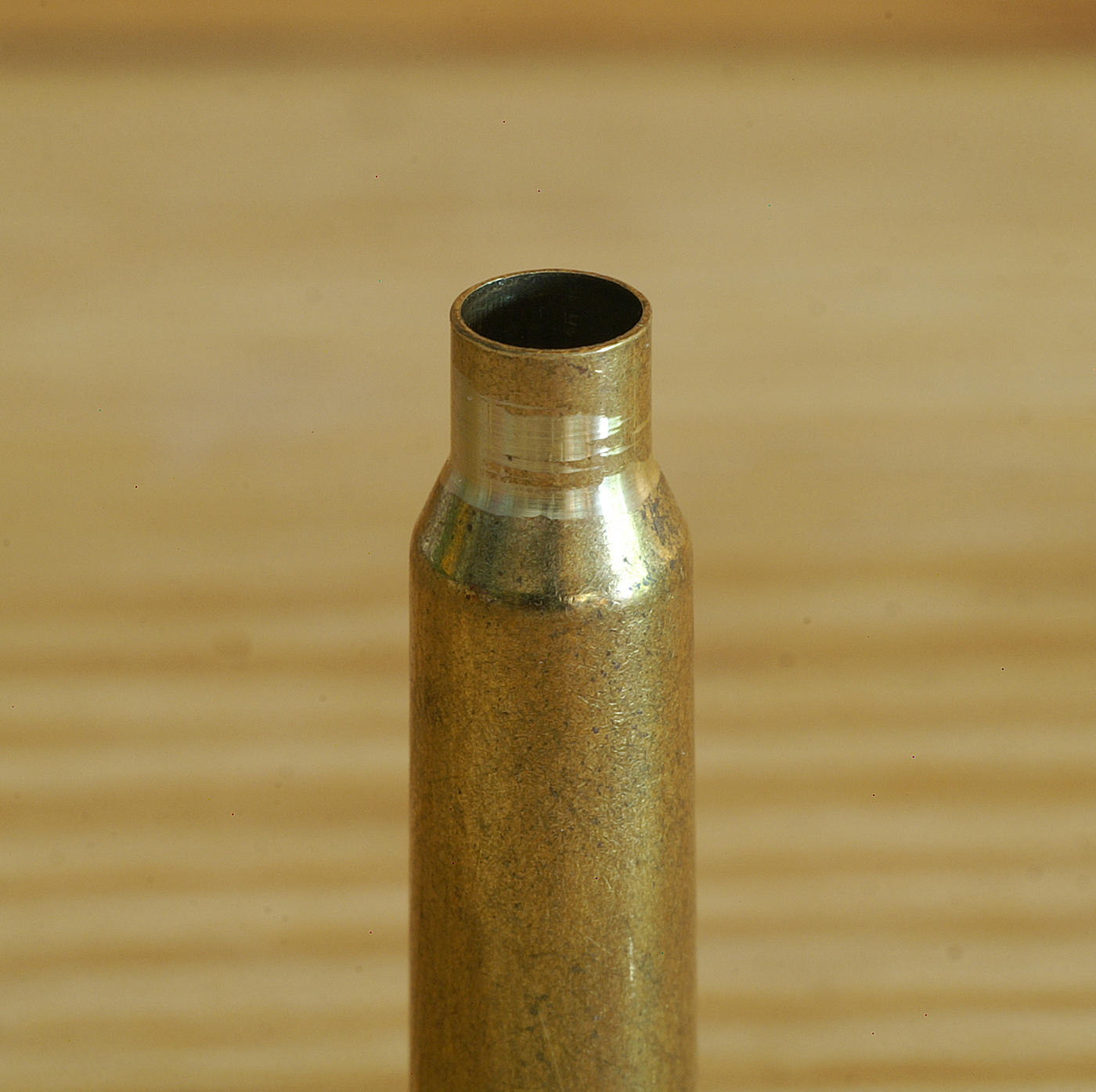
Check out neck turning tools at Midsouth. CLICK HERE.
The preceding was adapted from Glen’s newest book, Top-Grade Ammo, available here at Midsouth. For more information on this book, and others, plus articles and information for download, visit ZedikerPublishing.com