This is a specially-adapted excerpt from the forthcoming book, “Top Grade Ammo,” by author Glen Zediker, owner of Zediker Publishing. Click here to order from Midsouth.
by Glen Zediker
My approach to some topics has changed over the years. It used to be that I would state my version of the truth, and explain its origin, and that meant also that anything not said didn’t matter, to me, or to the advice and instruction I was set out to deliver. Well. The internet.
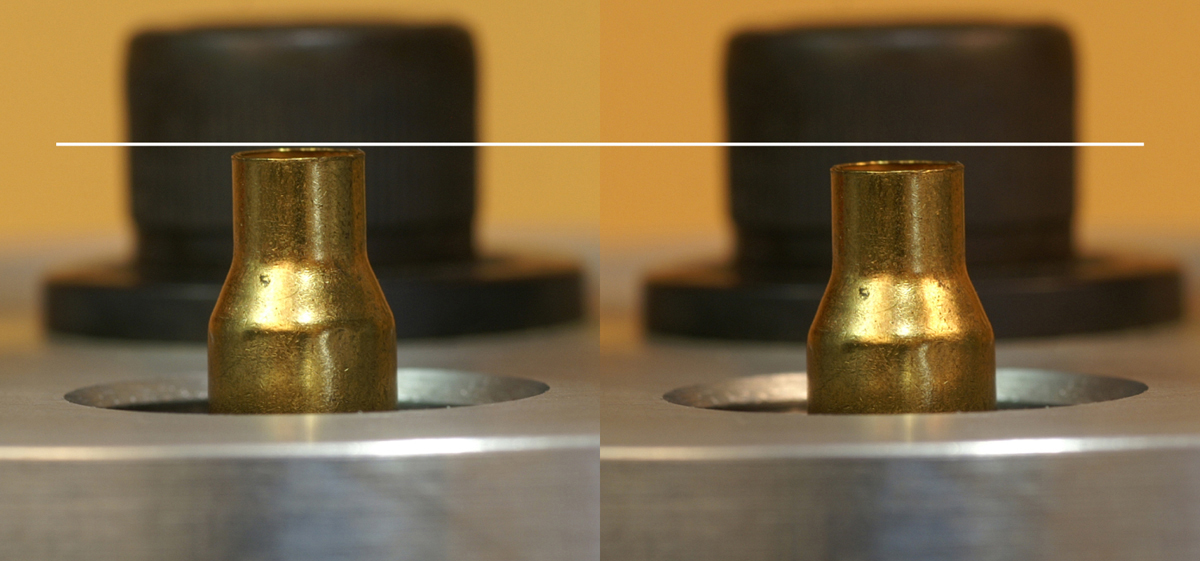
If you’ve kept up with the advice presented in this space on the better way to set up a case-sizing die, this next has already been dispelled, but judging from some of the emails I received asking questions, here’s a little more. I’ve fielded a few about “camming-over” a reloading press.
Some reloading presses, and RCBS comes first to mind, are designed with eccentric linkage. The concept involves circular motion and linear motion, meaning that when the ram traveling in a linear path reaches full extension, the linkage, which is traveling in a circular path, can move through the 0-degree mark and go to a negative degree. What that does is change the press ram position at the very top of its travel limit to a lower position. As the handle is drawn downward, the ram top reaches its maximum height and, at the last little bit, lowers. The amount varies in different designs. This action is an asset to attain flush-plus contact with the shellholder and the bottom of the sizing die, for them that wants it.
Now, any substantial press, whether it has eccentric linkage or not, can produce the effect of camming-over. A Forster Co-Ax, for good example, can just about crush a chrome bumper and doesn’t have eccentric linkage. To set up that press, any press, to cam-over, turn the sizing die downward beyond what provides full and flush contact with the shellholder when the ram is at its full height. Say, another 1/8 turn down.
Then, when the press handle is fully depressed, the additional pressure in the last bit of the handle stroke goes toward flexing the press. Simple as that, and that is what camming-over does: flex the press. That’s true whether it has eccentric linkage or not.
Don’t do it. Just don’t.
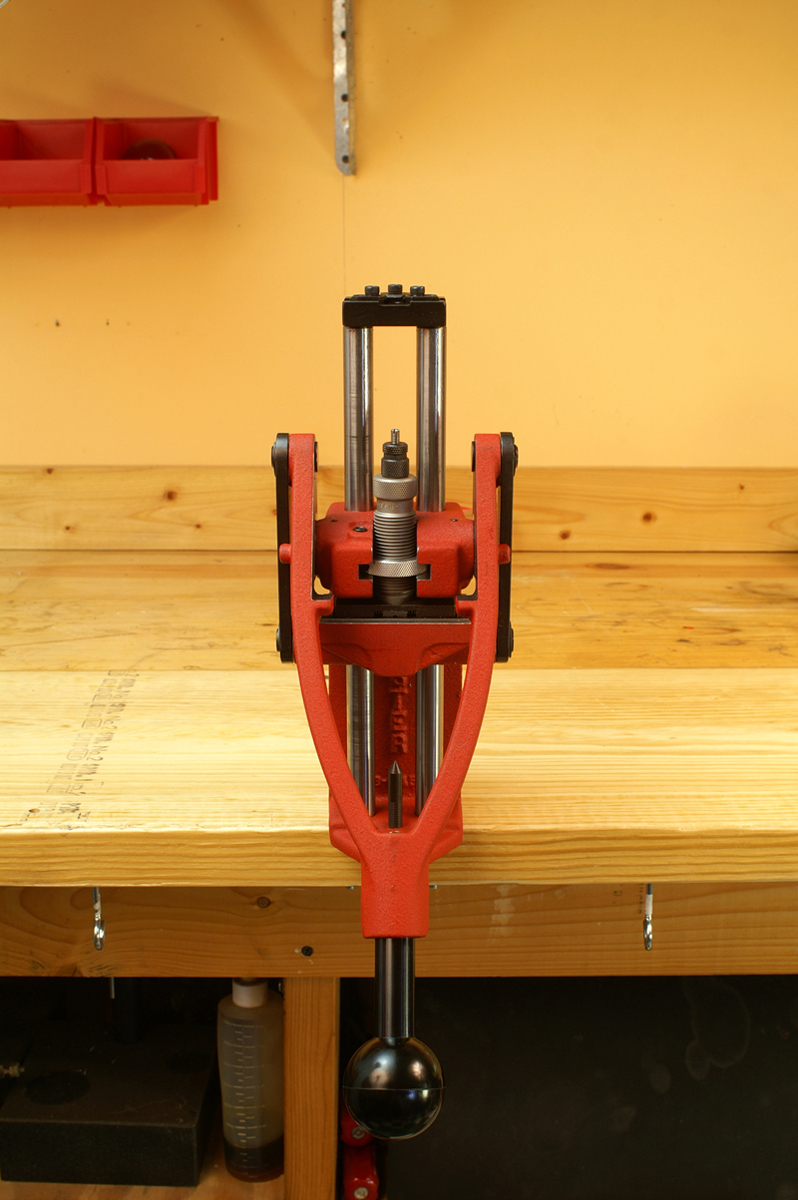
There’s no need to cam-over a press for a case-sizing operation. It stresses the machine and the tooling. Dies can get deformed and bent, carbide dies can break, and the press itself can suffer. I’ve known them to break. Some say that presses are designed to “take it,” but there’s an eventual penalty for repeatedly taking any machine to its limits. Ask any racer.
The main point is this: It’s not necessary. And it’s wrong. Going over the previous material on using a cartridge case headspace gage to determine sizing die positioning to get the correct amount of case shoulder setback, it’s clear that this sure should occur at a point shy of full contact of the die bottom and the shellholder surfaces. And, if it’s not enough, trying to push a case farther into the die by crushing the shellholder against the die isn’t going to do much. Folks. Done is done. The flexing might, maybe (maybe), increase setback 0.001.
If your sizing die doesn’t adequately set back a case shoulder, have a machinist remove metal from the die bottom. Best to use a surface grinder to avoid messing with the heat-treat on the die.
I’m rehashing a few things already covered because they’re germane to the whole camming tactic. Tooling manufacturers tend to suggest the “turn the die down to the shellholder, and then another xx-th turn…” to ensure that someone’s reloads are plenty short enough in headspace to fit any rifle made out there. As mentioned a few times back, I applied that tactic with a new Forster Full-Length .223 Rem. die (without adding any extra down-turns to cam-over the press) and that netted 0.008 additional case shoulder height reduction on a new, unfired commercial case. A foolish amount, in my belief. Since I then adjusted the die to provide 0.004 setback from fired, which was 0.002 taller than the new case read (on my headspace gage), it’s clear that this die is not touching the shellholder to produce well-beyond-safe shoulder reduction. One-eighth turn is about 0.009 inches.
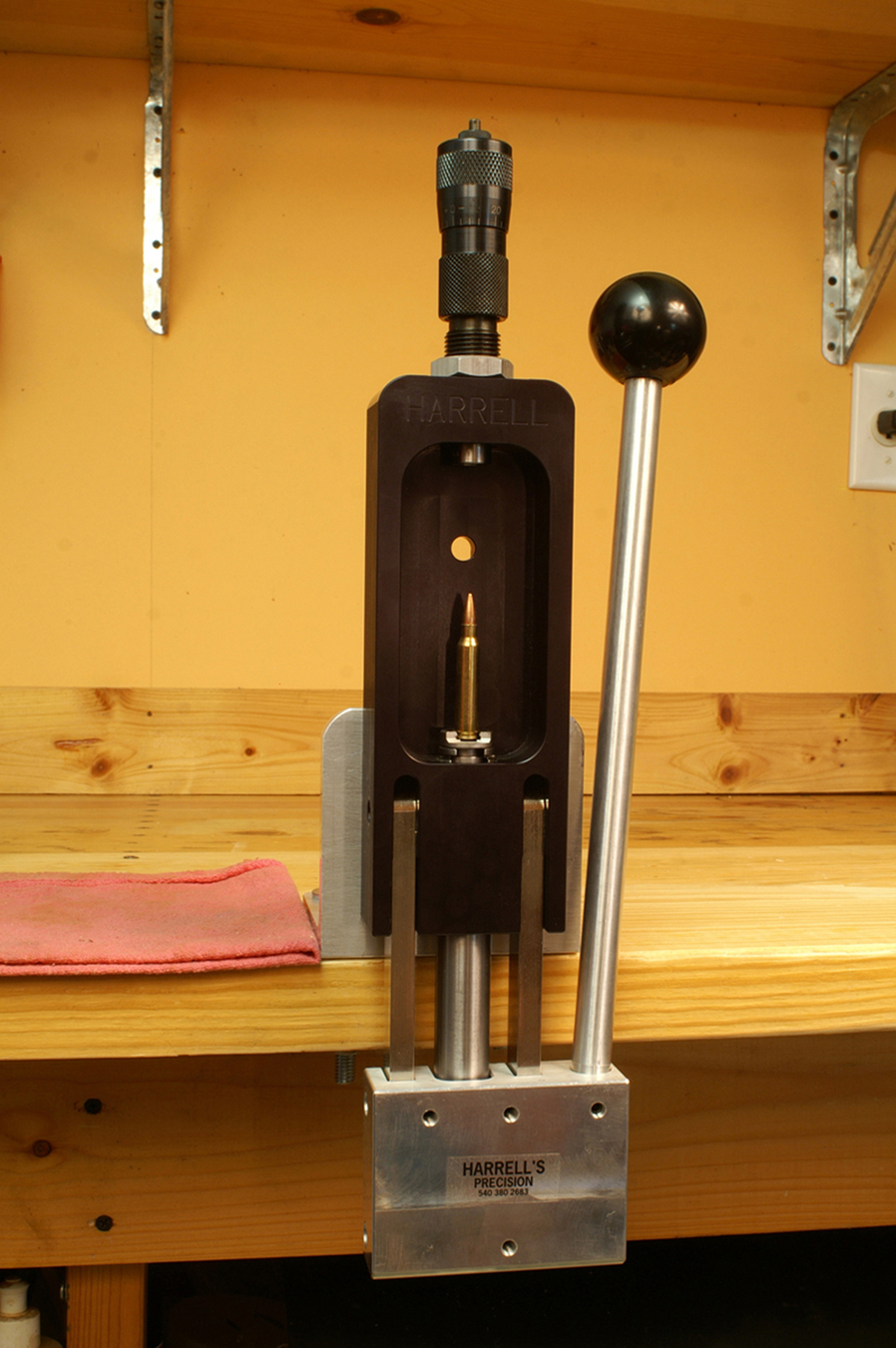
To find out if you have a “cammer,” run the press ram fully up (press handle fully down) and thread a die in until it touches the shellholder. Try to move the handle back down. If it won’t budge, it’s got eccentric linkage. It won’t move because the ram is trying raise again. Back out the die until the handle moves and pulls the ram away. It’s at this point where “flush” contact with a die bottom will be.
Camming-over a press is a “feel-good” measure for some folks: there’s this satisfying “ka-thunk” at the bottoming limit of press handle stroke, and that lets a loader know that he or she gave it all they could get. It’s just going to be too much. The only time it’s not is for bullet swaging operations, but those aren’t on my list.